|
It’s hard to talk to Michael Brown without hearing a thing or two about cars. Brown’s grandfather spent thirty-six years on a production line at GM and his father logged thirty-four. That means the family garage was always full of new cars, including Corvettes and a 1987 Buick Regal Grand National. The latter, Brown says, could have beat a C4 on a racetrack if GM’s marketing team would have allowed it.
Brown’s knowledge of cars goes beyond trivia, pride, and passion—the automotive industry was his first love. After studying business administration, logistics, and supply chain management, he spent fourteen years managing materials and logistics at Chrysler (now Stellantis).
The lessons he learned and the time he spent in a challenging, cyclical, and volatile industry informs how he manages supply chain operations and environmental services at one of the top children’s hospitals in the nation.
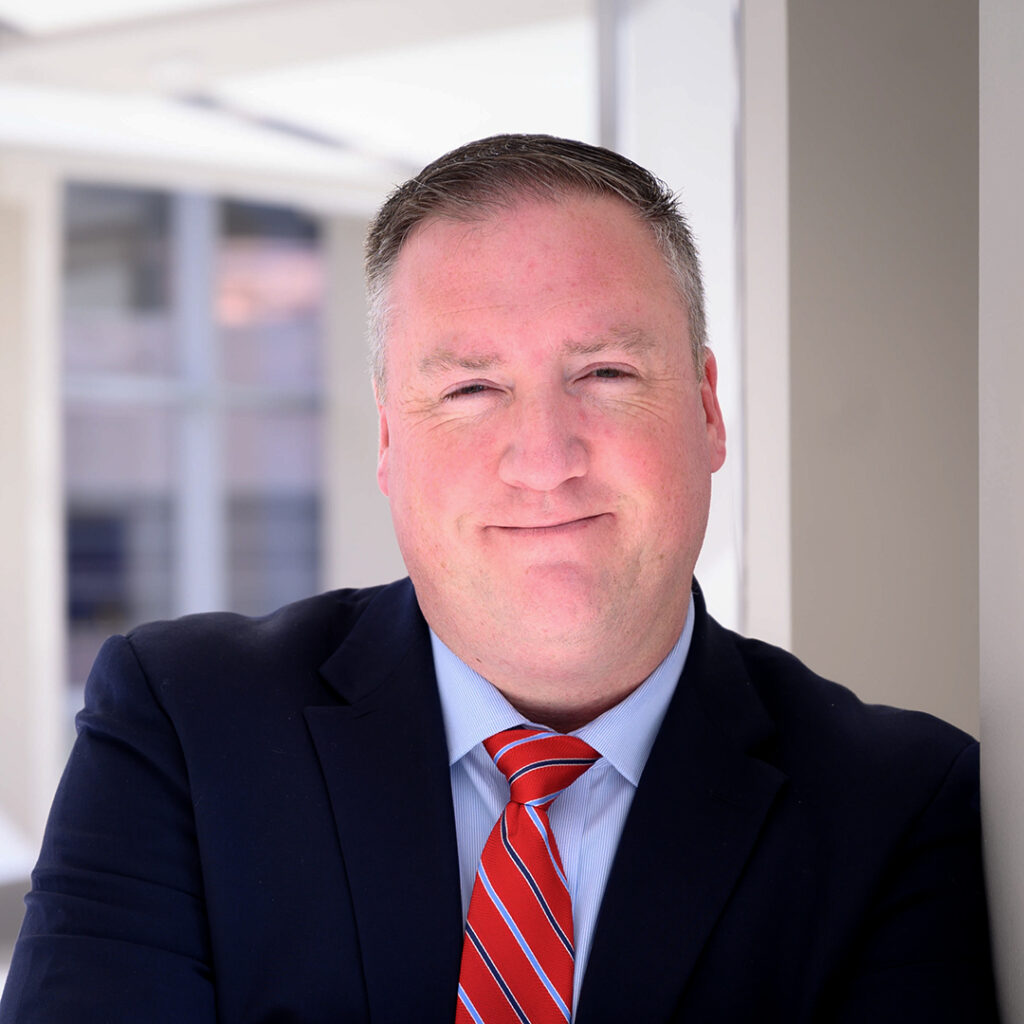
“Supply chains get stuck when there are twenty people working on twenty projects. I wanted twenty people completing two projects, and then moving on to the next two, and so on.”
—Michael Brown
The organization, Texas Children’s Hospital, hosts over 4.3 million patient encounters in various locations across greater Houston each year. Its patients are some of the most sick and vulnerable children in the world. Brown and the 750 people he leads work behind the scenes to ensure the care teams who treat every one of those kids and women have the products, medicines, supplies, and clean environments they need to drive positive outcomes.
Roles with Cleveland Clinic and City of Hope helped Michael Brown get experience in his new industry before he moved to Houston. He joined Texas Children’s five years ago, and immediately saw an opportunity to leverage best practices from the automotive world. Today he’s the vice president of supply chain operations and environmental services.
“I started with the intent to bring a constant focus on standardization and use the power of technology,” says Brown, adding that he’s only recently seen supply chain managers in healthcare use tools like advance shipping notice. ASN has been the standard at automakers since the late 1990s.

“We have to embrace tech solutions faster to make processes more productive, provide better care for patients, and drive more value to the organization,” the VP says.
That’s become his own personal mission. Brown started implementing what he calls “resetting basic conditions” to get the right leaders in the right spot focused on the right things. “Supply chains get stuck when there are twenty people working on twenty projects,” he says. “I wanted twenty people completing two projects, and then moving on to the next and so on.”
First, Michael Brown moved product distribution to a new prime vendor to capture financial savings and operational benefits. Then, he established leadership positions for strategic sourcing to centralize pricing and contract negotiation. He expanded clinical value analysis to support a growing organization through an ever-changing vendor landscape. That move grew that one team from two to more than fourteen people.
Strong support from key leaders has helped others embrace what Brown is doing to elevate supply chain operations. He credits advocates like President and CEO Mark A. Wallace with setting the tone. Wallace is a trusted voice, who has been part of the Texas Medical Center community for forty-five years and Texas Children’s president and CEO for the last thirty-three.
“We didn’t just think outside of the box. We went so far outside of the box we couldn’t even see the box anymore.”
Michael Brown
Brown also built strong relationships with clinicians. He recruited nurses, physicians, and others to help his team source, identify, and select the best tools for every job.
Of course, the COVID-19 pandemic changed everything in healthcare and impacted supply chain operations worldwide. In early 2020, Texas Children’s leaders transformed a conference room into a logistics subcommand to resolve product and service challenges across the system and locate masks, gowns, hand sanitizer, plexiglass, and other critical supplies. Although it was a trying time, Brown says he saw the very best of Texas Children’s culture come alive. His peers worked outside of traditional functions to find new ways to wire money and buy directly from new vendors overseas.
“We didn’t just think outside of the box. We went so far outside of the box we couldn’t even see the box anymore,” Michael Brown says. His team petitioned a local oil and gas company to make medical gowns from plastic sheeting. A Houston-based whiskey company converted their lines to make hand sanitizer. Hospital employees had to make special dispensers to accommodate the homemade substance.
As the pandemic subsides, Brown is analyzing the landscape to determine which emergency practices will stay. Hospitals have had to shift from a “just in time” inventory practice to one of “just in case.” That means Texas Children’s will hold thirty to forty-five days of supplies, instead of the traditional fifteen.
He’s also working more closely with vendors to minimize risk, smoothing out a new ERP, thinking about ways to drive costs down, and preparing to implement a warehouse management system.
Texas Children’s is bringing a fifty-two-bed children and women’s hospital to the central part of the state. The 365,000-square-foot facility will feature operating rooms, intensive care units, an emergency center, and a high-risk delivery unit. A strong supply chain helps make it all possible.
“We don’t always get to meet patients,” Michael Brown says. “But when we open new buildings and support the care that goes on inside, we know we’re making things better for patients and their families. And that’s our number one goal.”
Editor’s Note: Texas Children’s Hospital North Austin Campus will open in 2024.