The complexity of clinical studies is mind-boggling. In addition to the scientific foundation of any particular hypothesis and the technical planning that underpins each inquiry, there are countless external factors that can impact their success. Uncertainty surrounding geopolitical issues such as Brexit, for example, can impact factors like the accessibility and distribution methods of study medicines. Changes in associated import/export taxes can render established budgets obsolete. Expanding trials to multiple global study sites can introduce unanticipated rules and regulations that complicate supply chain and logistics strategies. Or simple delays in enrolling adequate numbers of eligible study subjects can create issues related to product expiration.
All of those complications occur in areas where Fisher Clinical Services excels. As a leader in clinical supply chain management, the company has the experience and expertise to handle nearly every conceivable inventory management, packaging, and distribution challenge associated with worldwide clinical trials that their clients might encounter.
Fisher Clinical Services, by Thermo Fisher Scientific, has access to the resources and capabilities of Patheon, a contract development and manufacturing organization, that was acquired in 2017. In addition to more traditional supply chain management tasks, the company can address manufacturing needs, such as synthesizing new drug formulations, creating stability studies, or developing new drug protocols.
According to Sylvia Tsengouras, Fisher Clinical Services’ senior clinical supply chain manager, effective supply chain management starts with five things:
- Preparing a strategic plan to develop and managing adequate inventory
- Implementing appropriate labeling and packaging designs
- Assuring flexible distribution
- Confirming an adequately programmed dispensing system
- Developing risk mitigation strategies for each component and stage of the study
However, companies often have multiple products in development at once, so they may not have the resources to support all these activities. Limited financial resources may make manufacturing on a large scale impossible; therefore, planning for limited quantities often becomes the first challenge.
“We have to forecast details down to the individual tablet to ensure adequate supply for all our clients’ study sites,” Tsengouras says.
For example, it may require one hundred sites to identify, screen, and enroll a total of fifty eligible subjects. Although not every site will enroll a subject, and others may enroll more than one, every site must have an adequate amount of supplies. Supply depots must have contingencies and additional supplies in place to distribute medications in a timely manner, Tsengouras says.
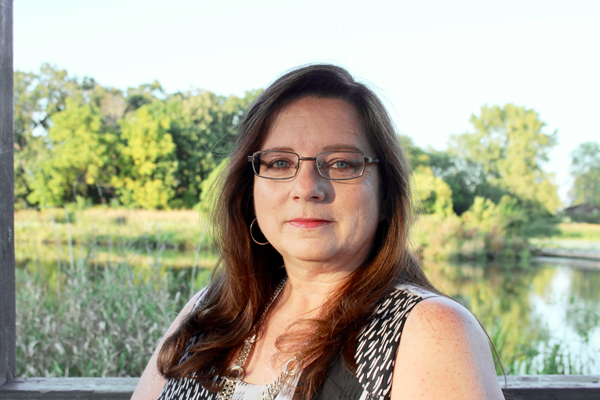
This is critical because delays in reaching enrollment targets can have ripple effects on a company’s supply chain. Extending a study by six months requires additional financial investment and can impact drug storage because of expiration deadlines and compliance with local regulations.
“We make every effort to anticipate any issue that might impact clinical supply,” Tsengouras says. “It’s a matter of planning ahead, then thinking on your feet and acting efficiently to take quick action when necessary.”
To help ensure the accuracy of supply chain forecasting—everything from appropriate manufacturing volume to managing expiry dates—Tsengouras works with specialized internal teams that utilize simulation tools to develop various logistic scenarios along with the most effective solutions. That level of insight is aligned throughout the company’s fully integrated global network, which includes Fisher Clinical Services experts that are familiar with regional regulations and compliance, and have relationships with local customs officials. This provides capabilities to address nearly every possible contingency.
With all its experience and extended capabilities, she points out that Fisher Clinical Services can serve the needs of clients ranging from start-ups to pharmaceutical giants. An emerging company consisting of a single team of scientists that has achieved positive laboratory and preclinical tests might need to convert a tablet formulation to liquid for trials with children, or to develop easy-open packaging for an elderly population.
On the other hand, a legacy company might want to redeploy internal resources away from compounds that have already been in active development. Fisher Clinical Services offerings are able to handle manufacturing, supply management, packaging, labeling, and distribution to investigator sites. Although Tsengouras has clocked years of experience dealing with every minor detail of the healthcare supply chain, there are still some moments that stick out to her as particularly unexpected.
Years before she joined Fisher Clinical Services, Tsengouras faced one of the most challenging unanticipated issues of her career, she says. A massive flood destroyed the first floor of a packaging and storage facility, wiping out $1 million in supplies that impacted more than twenty ongoing clinical programs. She was able to save about $2 to $3 million of her company’s product, which she had moved to a secure facility and tested for integrity and purity. The remaining supplies were available for use within a month.
One of Tsengouras’ newest challenges is adhering to the stringent temperature requirements of new biologic compounds. This requires ensuring materials remain refrigerated or frozen within a narrow window of variation. “Through extensive planning, employing specific types of shipping containers, knowing the conditions we’ll encounter, and constant monitoring, we can maintain and protect the integrity of every shipment from end-to-end,” Tsengouras says.
“Regardless of their size, we help our clients get the best possible outcomes for their clinical trials—no matter what unexpected events might come up along the way,” Tsengouras says.